

Straight-tube, fixed tubesheet heat exchanger types are the most common and, generally, least expensive designs. Straight-Tube, Fixed Tubesheet Type Heat Exchangers
#TEMA TYPE EXCHANGERS CODE#
The designation types use a letter code for each of the front-end, shell and rear-end types. This table, from the TEMA standard, shows the available combinations of exchanger components. Another example is an AES type, which has a bolted front channel with removable cover, a single-pass shell and a floating rear tubesheet.įIGURE 1.
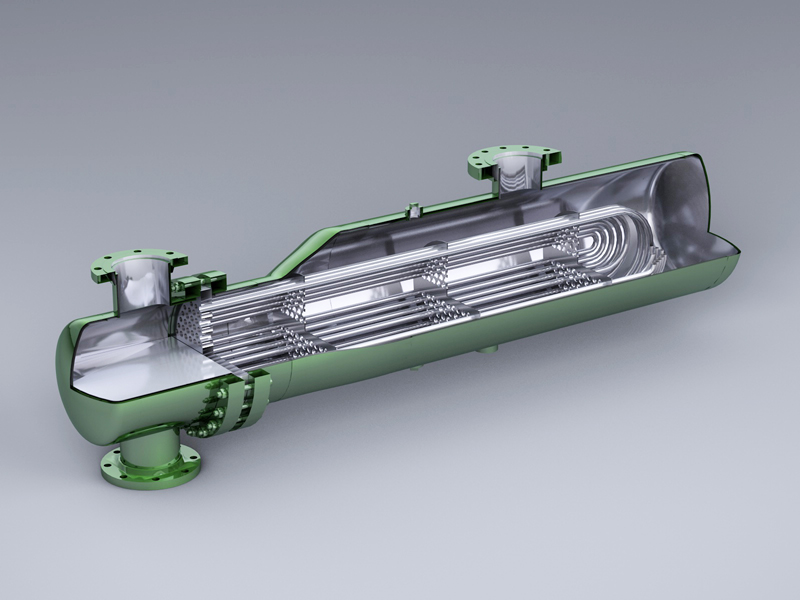
It has a bolted bonnet on each end, fixed tubesheets and a single-pass shell section. The TEMA standard also defines the classes and main configuration styles of exchangers.įigure 1 shows the available combinations of exchanger components from the TEMA standard. This standard and the ASME code are the main standards used to design and fabricate exchangers along with any applicable customer specifications. The Tubular Exchanger Manufacturers Association, or TEMA, publishes a standard that establishes design, fabrication, tolerances, installation and maintenance of shell-and-tube type exchangers. This article provides information on several of the most widely used configurations and briefly discusses some of the issues to consider when planning for and selecting a heat exchanger configuration. There are advantages and disadvantages to each design, depending on factors such as process and thermal requirements, available space, financial budget and cleaning requirements. Many different configurations of shell-and-tube heat exchangers are available.

This step determines the thickness of all parts as well as welding details required for the temperature and pressure conditions. Other factors considered at this stage include allowable pressure drop through the exchanger, any space constraints on the unit, the potential fouling of the unit and any resulting flow-induced vibration from the proposed design.Īfter the exchanger size is determined by the thermal design, a mechanical design is performed. Given the process conditions and heat transfer requirements, the thermal design determines the exchanger’s size, shape, number and size of tubes, number of baffles and baffle pitch, etc. For most shell-and-tube heat exchanger types, the first step in designing an exchanger for a specific process is thermal design.
